-
Financial statements audits
Financial statements audits
-
Financial statement reviews
Financial statement reviews
-
Financial statements compilations
Financial statements compilations
-
IFRS
IFRS
-
Audit quality monitoring
Audit quality monitoring
-
Global audit technology
Global audit technology
-
Systems and risk assurance
Systems and risk assurance
-
General business consulting
General business consulting
-
Market research
Market research
-
Sustainability
Sustainability is indeed a broad concept. Aside from mitigating the environmental changes caused by the interaction of the industrial world and society with nature, social and governance matters are subjected to increased public and government scrutiny, calling for the promotion of a sustainable performance agenda.
-
Business planning and performance improvement
Business planning and performance improvement
-
Change and program management
Change and program management
-
Business intelligence and analytics
Business intelligence and analytics
-
Business valuation and litigation support
Business valuation and litigation support
-
Business process outsourcing and consulting
Business process outsourcing and consulting
-
Family business consulting
Our business solutions for family businesses center on alignment of all aspects of the family and business, including culture, vision, mission, values, governance, ownership, leadership, communication and policy development.
-
Quantitative small caps
Grant Thornton has a wide professional network with a vast array of technical skills that is coupled with a drive to understand the business problem; we can set up the most efficient financial risk management structure that fits your underlying business structure and your risk appetite.
-
Data analytics
Data analytics is the process through which businesses leverage data to gain actionable insights and enhance their performance. This is based on a solid foundation of well-organised and accurate data. Many businesses have a large amount of data at their disposal however, most of them do not have the expertise to analyse the available data.
-
Bookkeeping & financial accounting
Bookkeeping & financial accounting
-
Payroll and personnel administration
Payroll and personnel administration
-
Direct and Indirect tax compliance
Tax compliance within outsourcing
-
Compilation of financial statements
Compilation of financial statements
-
Business process outsourcing
Business process outsourcing including back office and secretarial
-
Family business consulting
Family business consulting
-
Startups
Startups
-
Company formation
Company formation
-
BOR
Entities in Malta, including companies, partnerships, foundations, trusts and associations, have an obligation to disclose the ultimate beneficial owner/s (physical person) of the entities. A beneficial owner is defined as the individual (s) who ultimately owns or controls a legal entity or arrangement through direct or indirect ownership of a sufficient percentage of the shares or voting rights or ownership interest in that entity.
-
Internal audit
Internal audit
-
Risk management and internal controls consulting
Risk management and internal controls consulting
-
Governance and risk management
Governance and risk management
-
Regulatory services
Regulatory services
-
Risk modelling services
Risk modelling services
-
Forensic and investigation
Forensic and investigation
-
Compliance audit
A compliance audit is a detailed review which focuses on whether an organisation is in conformity with statutory laws as well as internal rules and decisions. This type of audit also assesses the effectiveness of an organization’s internal controls by identifying weaknesses in compliance processes whilst finding measures to enhance such processes.
-
Citizenship by naturalisation
The Maltese Citizenship Act (Cap 188) establishes who may become a citizen of Malta by naturalisation, provided that the applicant satisfies the relative provisions.
-
Citizenship for Exceptional Services by Direct Investment
With the continuously changing global dynamics and evolving geopolitics, there is an ever-growing number of highly-talented high-net-worth individuals who are willing to invest and relocate to give themselves and their family members the chance to broaden their horizons and become part of a welcoming community.
-
Grant of Citizenship for Exceptional Services
Malta has enacted legislation which extends to individuals providing excellent or manifestly superior contributions in the fields of science, research, sports, arts and culture as well as people of exceptional interest to the Republic of Malta, the right to become Maltese citizens.
-
Acquisition of citizenship by registration
The Maltese Citizenship Act (Cap 188) establishes who can register as a citizens of Malta. The Act was amended on 1st August 2007, this making it possible for second and subsequent generations born abroad to acquire Maltese citizenship by registration.
-
Maltese Family Businesses Resource Centre
For over 30 years Grant Thornton’s advisory teams have assisted family businesses in navigating the challenges of leadership and succession across generations
-
Grooming
Preparing the next generation for leadership and ownership is an integral part of any succession process. Grant Thornton can help formulate the necessary grooming plan for all the potential successors.
-
Tax services
Using a combination of reason and instinct, we can work with clients to develop a strategy that helps them understand and manage their tax liability in a transparent and ethical way.
-
Governance
Having a proper governance structure is essential to ensure that the family and business strategies are achieved. Grant Thornton can advise on this, and facilitate the implementation of the ideal governance structure based on the exact scenario.
-
Ownership succession
Letting go of your family business is difficult for all owners and even more so for founders; however, in a family business the additional challenge presented by the family component increases the complexity of this process. Our team of family business advisors will ensure that such ownership issues are dealt with in an effective and structured approach.
-
Exit strategies
There are many 'exit strategies' that need to be considered to minimise the risk of conflict. They can arise from the eventual exit of a family member from the ownership ranks and can have many causes. See how we can help.
-
Management succession
By implementing our family business guidelines to family succession and a proper governance structure, the management succession process can be completed with minimal conflict and will result in the most competent successor being chosen.
-
Shaping Malta's Future: GenAI
Join our exclusive GenAI Design Thinking Workshop with Microsoft and industry leaders. Gain practical insights, explore real-world AI use cases, and leave with a blueprint for your next AI-driven innovation - potentially 100% funded by Microsoft!
-
DORA Consultancy
Firms within the financial sector face a critical imperative to fortify their operational resilience in the digital sphere. Get ahead & prepare for DORA!
-
Cyber security Consultancy
Whether you are a multinational corporation, a small business, or an individual, the digital realm holds equal importance for us all.
-
Digital Transformation
Build a solid foundation to fuel business reinvention and gain the flexibility you need to succeed through digital transformation.
-
IT Audit and Assurance
Information systems procedures have evolved drastically, but so have hacking techniques. Assess your IT resilience & protect your firm!
-
Fintech and Innovation
Are you ready to explore the fintech space? Grant Thornton is able to guide you from start to finish.
-
Case Studies
Digital transformation has transitioned from being an option to a necessity. The race is on... The question is, are you ready?
-
Operational and financial restructuring and reorganisation
Operational and financial restructuring and reorganisation
-
Recovery
Recovery
-
Financial regulatory services
Financial regulatory services
-
GDPR consultancy
The General Data Protection Regulations (GDPR) have transformed the way we handle personal data. This regulation is a game-changer for businesses operating within the EU, or the handling of EU citizens' data worldwide.
-
Ship and aircraft registration
Ship and aircraft registration
-
Medical cannabis licensing in Malta
A study published in 2018 by market intelligence and strategic consultancy firm Prohibition Partners, has forecasted that the European cannabis market will be valued €115.7 billion by 2028. According to the same study, while patient numbers are currently below 100,000 across the region, their number is set to grow to over 30 million in the next decade. In 2018 Malta introduced a bill to legalise the use of medical marijuana and attract companies willing to produce high-grade medical cannabis for the European market.
-
Trust and trustee services
As an entrepreneur, business owner, parent or guardian, you will want to ensure that whatever happens in the future, the rewards from your hard work can be protected as efficiently as possible. Grant Thornton Fiduciaire Limited (Grant Thornton) understands this and provides a professional and holistic trust management service.
-
Family trusts
The law establishes the requirement of a license for one to be able to act as a trustee subject to certain limited exceptions. One such exception is found in the Rules for Trustees of Family Trusts which provide for an exception to this rule where a trust is set up to hold property settled by a settlor or settlors for the present and future needs of family members or of family dependants who are clearly identifiable.
-
Programmes
Grant Thornton is authorised and regulated by the Government of Malta to handle and submit applications for both citizenship applications as well as residence permits under the various residence programmes available in terms of Maltese law.
-
Ordinary residency in Malta
Any EU, EEA or third country national who resides in Malta for more than 3 months is obliged to apply for a Residence Permit. There are various grounds upon which an applicant may apply to require a residence permit, including: Self-Sufficiency, Employment or Self-Employment, Family Members, Permanent Residence, Study Purposes.
-
Qualifying Employment in Aviation Rule
Malta provides qualified persons employed in the field of aviation with an opportunity to enjoy a 15% flat personal tax rate on income generated from their direct employment in Malta. For a candidate to qualify, their annual income must exceed €45,000. This does not include the value of fringe benefits and applies to the derived income received from an eligible office.
-
Qualifying Employment in Innovation and Creativity (Personal Tax) (Amendment) Rules, 2019
These Rules allows persons employed in a role directly engaged in carrying out, or management of research, development, design, analytical or innovation activities, to enjoy a 15% flat personal tax rate on income generated from their direct employment in Malta.
-
Qualifying Employment in Maritime and Offshore Oil & Gas Industry Rule
Malta provides qualified persons employed in the field of aviation, with an opportunity to enjoy a 15% flat personal tax rate on income generated from their direct employment in Malta.
-
Nomad Residence Permit
The NOMAD residence permit, which was launched in June 2021, allows third-country nationals who would normally require a Visa to travel to Malta, to retain their current employment based in another country whilst legally residing on the island.
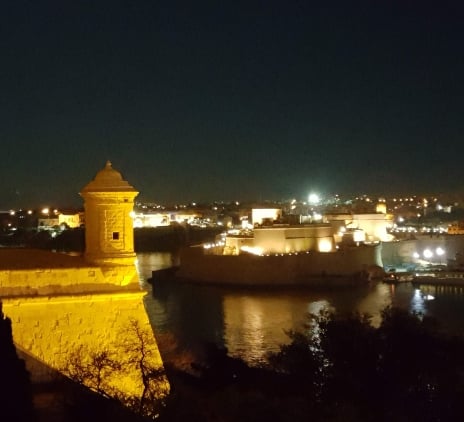
-
Direct international tax
Direct international tax
-
Indirect international tax
Indirect international tax
-
Global mobility services
Global mobility services
-
Transfer pricing
Transfer pricing
-
Estate planning
Estate planning
-
Wealth advisory
Wealth advisory
-
Regulatory and legal
Regulatory and legal
-
Corporate tax services
Corporate services
-
VAT
At its simplest, VAT is a tax on consumption and is a multi-stage tax (ie applied at every stage of the production process), which is applied to both goods (ie tangible property) and services. Additionally, although the tax is ultimately borne by the consumer (by getting included in the price paid), responsibility for charging, collecting and passing the tax on to the tax authorities, rests with the supplier.
-
2018 Amendments of the Income Tax Act
The following is a brief overview of the new tax provisions introduced in 2018 by the Budget Implementation Act (Act VII of 2018) and other legislative enactments
-
Mergers and acquisitions
Mergers and acquisitions
-
ESEF Reporting
Our ESEF reporting service is tailored to assist listed companies in complying with the European Single Electronic Format (ESEF) requirements. As of 2020, ESEF is mandated for annual financial reports of issuers with securities listed on regulated markets. We provide services for mapping the taxonomy and generating audit/regulator-ready xHTML reports.
-
Prospects MTF
As of 2016, small and medium-sized enterprises in Malta can access the capital markets through Prospects - a market of the Malta Stock Exchange (MSE) designed specifically for Small and Medium sized Enterprises (SME). Prospects offers a cost-effective opportunity for entities looking to raise up to €5 million per issue.
-
Project financing
Project financing
-
Due diligence
Due diligence
-
Valuations
Valuations
-
Foreign direct investment
Foreign direct investment (FDI) is the category of international investment that echoes the objective of obtaining a lasting interest by an investor in one economy in an enterprise resident in another economy.
-
Wholesale Securities Market
WSM is a joint venture between the Malta Stock Exchange and the Irish Stock Exchange, combining the best of each partner’s processes and technical skills.
-
Aviation
The Maltese Government is constantly remaining to improve the position as the best place to do business within the aviation industry through exhaustive tax agreements, powerful legislation, and many aviation professionals. This is the best time for airlines, financiers and aircraft owners to be located in Malta.
-
Maritime
For Maritime, Grant Thornton provide direction with regards to VAT guidelines for yacht leasing, as well as ship and aircraft registration.
-
Automotive
We offer a broad range of services relating to automotive, ranging from Transaction advisory, access to finance, business advisory, process and inventory management, tax advisory, audit and advisory, outsourced support services.
-
Gaming Regulations
Malta recently overhauled the framework regulating the iGaming sector. Going forward operators will still be required to obtain authorisation to carry out regulated activities.
-
Licensing Process
Prior to submission all applicants are advised to go through a pre-application process with one of the MGA’s Licensing Officers. This will ensure that the application has been correctly compiled and all the key ingredients are present.
-
Malta Real Estate Investment Trust (REIT)
As part of the 2019 budget, the government has pledged to introduce a Real Estate Investment Trust (REIT) framework in Malta.
-
The Markets in Financial Instruments Directive (MiFID) II
MiFID II aims to protect investors and make sure that financial markets operate in the fairest and most transparent way possible. Building on stock and investment trading regulation introduced in 2007 it sets to ensure a more integrated financial market.
-
Fintech and Innovation
At Grant Thornton we help innovative firms and entities operating in the fintech space launch new propositions and grow their business. We also help established businesses transform and take advantage of the fintech revolution.
-
Asset Management
At Grant Thornton we help innovative firms and entities operating in the fintech space launch new propositions and grow their business. We also help established businesses transform and take advantage of the fintech revolution.
-
Banking
Grant Thornton combines local insight with global scale to help banks meet regulatory expectations, improve technology, and finance the right companies. If you’re looking for a partner in the banking industry, our expertise can make a difference
Article originally published on www.grantthornton.com
The COVID-19 pandemic is upending the carefully calibrated logistics of global shipping and highlighting long-standing concerns. Plunging exports from China and congestion at Chinese ports are disrupting the trade of American goods. US farm products destined for Asian markets are stuck at Chinese ports, creating a traffic jam that is driving up prices for US exporters and sowing additional turmoil on top of a not-yet-resolved trade war. Factory shutdowns have crippled China’s industrial production. As a result, shipping volumes out of China have fallen.
A record 2 million containers of ocean-going cargo stalled in February, per Alphaliner – a Paris based marine data provider. That February number is higher than the 1.5 million in cargo idled in 2009 during the height of the Great Recession. Delivery issues; rising concerns around product availability, cost, and quality; and decreased manufacturing capacity stemming from plant closures and workforce shortages are all disrupting supply chains. While the ultimate effects of the COVID-19 crisis can’t be known yet, there is no question COVID-19 threatens the supply chains of both small and large organizations around the globe.
In the March 4, 2020 edition of Grant Thornton’s Economic Currents, Grant Thornton Chief Economist Diane Swonk discussed how COVID-19, combined with business investment decline, corporate debt levels, and low unemployment figures, could drop global GDP into recession. COVID-19 is directly suppressing growth on a global scale at sufficient magnitude to drive down GDP forecasts. Declines in travel and consumer spending support that projection.
Organizations need to act now to improve supply chain resilience and mitigate evolving constraints and related financial performance issues. They must focus organizational resources on the most important value protection and cash management efforts and determine whether this is the time to implement their business continuity plans and crisis management teams. They need to define the immediate, critical resiliency responses required to boost corporate performance, viability and sustainability. Supply chain disruptions increase the likelihood of logistical, financial, and solvency concerns, especially in the absence of substantial working capital or ready access to credit. A lack of organizational resiliency presents an essential modern day challenge for today’s business leaders. Many organizations are not prepared for a pandemic event.
On March 11, 2020 the World Health Organization declared COVID-19 a full-blown global pandemic, with sustained transmission of COVID-19 within most, if not all, countries and widespread community transmission between individual persons. This will mean even greater business disruption and financial losses, along with rapid setbacks to global GDP forecasts. This pandemic may also cause sizeable workforce availability constraints, as employees stay home to protect themselves, care for family members or are placed under local health quarantine.
The COVID-19 crisis presents today’s business leaders with a challenge the global economy has not faced since the Spanish Flu pandemic, which occurred between 1918-20. The Spanish Flu infected up to one third of the world population, with a mortality rate of approximately 3%, killing many young adults in the prime of their lives. Over the subsequent 100 years, the growth engines driving business ecosystems have changed, becoming broadly global and dependent on trade across far-flung supply chains. These supply changes are finely tuned to manage raw material and production costs and to deliver competitively priced products to consumers. The time and cost variances of a pandemic shock would severely affect already fragile supply chains. Such a crisis heightens the need for organizations to be able to access, quantify and respond to supply chain risks in real time. Otherwise, supply chain disruptions increase the likelihood of logistical, financial and solvency concerns, especially in the absence of substantial working capital or ready access to credit. The lack of organizational resiliency in the face of a pandemic presents an essential challenge for today’s business leaders.
Following are eight supply chain lessons organizations can apply today to better understand, prepare for and combat the disruptions of the COVID-19 pandemic.
8 Lessons for Mitigating Supply Chain Disruptions
- Lesson 1: Build a supply chain risk management governance framework and link underlying processes and key risk triggers to a business continuity plan
- Governance framework should be documented with clear roles and responsibilities
- Scope and objectives and desired outputs should be clearly defined
- Resiliency planning and business continuity must be included and tested
- The cadence for executive-level review should be firm and the results documented
- Lesson 2: Collect internal data on disruptions
- Data on prior events or disruptions is valuable. It can help predict results for future events
- The necessary data often has to be built rather than extracted from internal systems
- Challenge employees to identify events and train them on inputting and generating the kind of data that is needed
- Catalog the data for quick reference and better usability within qualitative and quantitative analysis and reporting
- Lesson 3: Leverage external data and models
- External data is equally important and useful for augmenting internal data
- Industry-specific data is often available and offers an added filter
- Cross-industry or customer consortiums offer unique data that adds context
- External models exist and can help validate internal data and findings
- Lesson 4: Identify the most prevalent supply chain risks
- Brainstorm with your internal thought leaders to identify the most obvious risk factors
- Consider the industry and competitors to identify other potential risk factors
- Subscribe to academic studies on risk factors in specific industries or geographies
- Think about risk factors that occur less frequently (e.g., natural disasters, trade wars, COVID-19)
- Imagine the art of the possible and run a few scenarios to see what happens
- Lesson 5: Conduct a supply chain risk assessment to understand the business impact of supply chain disruptions both upstream, internal and downstream, across various supplier groups and product lines
- Use the risk factors you identify to brainstorm the possible failure modes. For example, consider order and sources of potential disruptions, cost of parts, products and other variable costs, workforce stoppage costs due to supplier non-performance, or non-performance due to supplier workforce stoppage or slowdown.
- Allow all key stakeholders to build their own risk-based view driven by their first-hand view of possible failures and root cause analysis
- Consider denial of use or premises in the risk assessment. Apply varying time durations
- Socialize and reach consensus on the possible root causes and impact zones
- Complete quantitative scoring of the impact models
- Lesson 6: Use quantitative modeling that evaluates supply chain risks based on conditional probabilities
- Build quantitative models that can learn from valid data you collect and maintain
- Integrate your risk assessment and cost analysis into the risk modeling
- Use scenario modeling, root cause analysis, and correlations to test the impact zones for unrelated events across different manufacturing, delivery and quality aspects of your supply chain
- Use algorithms tuned to evaluate emerging and atypical risks and adjust accordingly
- Lesson 7: Develop and iterate on your resiliency plans including a disaster recovery plan with business rules that determine when these plans go into effect
- Always understand the financial exposure you assume with your supply chain subject to the likelihood such exposure actually occurs
- Align resources with the most critical resiliency plans that also protect your working capital
- Build detailed resiliency plans as part of your supply chain risk governance framework
- Maintain disaster recovery plans with clear initiation triggers and guidelines
- Lesson 8: Demand that your suppliers, contract manufacturers, 3PL providers, and other have sophisticated supply chain risk management and resiliency planning capabilities
- Your upstream and downstream trading partners also have supply chain risks
- Ensure risk management and resiliency planning are part of your supplier management strategy
- Integrate supplier performance data into your risk modeling efforts
- Proactively search the relationships between variables
We are here to help you
We will keep on publishing updates as soon as they are made public. In the meantime, you can get in touch with one of our experts, who will be able to discuss with you how the above measures will affect your organization and guide you accordingly.
Another good way to keep in touch with us is to subscribe to our newsletter using the dedicated link below.